How a less energy-intensive process than the Haber–Bosch could slash carbon dioxide emissions from fertiliser production
-
Download this
Use this story and the accompanying summary slide for a real-world context when studying the Haber process and ammonia production with your 14–16 learners.
Download the story as MS Word or PDF and the summary slide as MS PowerPoint or PDF.
Lasers could offer a new, greener route to manufacture ammonia. For the first time, researchers have used infrared lasers to break the nitrogen–nitrogen triple covalent bond, offering a less energy-intensive alternative to the Haber–Bosch process.
Ammonia has been used as a fertiliser since the early 1900s, and it still plays a vital role in supplying soil with the nitrogen needed to grow sufficient crops for the global population. It is currently made using the Haber–Bosch process, in which nitrogen and hydrogen are reacted together at high temperatures and pressures with the aid of a catalyst. The Haber–Bosch process is so energy intensive that the fossil fuels used to power it cause about 1.5% of global carbon dioxide emissions.
Many researchers are looking for new ways to manufacture ammonia that are less harmful to our planet. Methods they are exploring include using electrochemistry and initiating nitrogen fixation with mechanical forces (a process called mechanochemistry). So far, none of these approaches meet the yield and other criteria needed to rival the Haber–Bosch process.
The green light
The research team behind this laser-based approach to nitrogen fixation start with lithium oxide. They use an infrared laser to break the lithium–oxygen bonds to produce metallic lithium. This lithium then spontaneously reacts with nitrogen in air to form lithium nitride. The scientists then hydrolyse the lithium nitride to produce ammonia and lithium hydroxide.
The team found that their laser-based approach yields two orders of magnitude more ammonia than other state-of-the-art manufacturing methods that also work at room temperature and atmospheric pressure. Additionally, the lithium hydroxide it produces is not a waste product. ‘A laser [can] induce the conversion of lithium hydroxide back into lithium nitride, effectively closing the lithium cycle,’ explains team member Huize Wang, from the Helmholtz Institute Erlangen-Nürnberg for Renewable Energy in Germany.
The scientists need to do some further work to scale up and perfect the process. They say their method may be particularly well suited for making relatively small amounts of ammonia at local manufacturing plants. Producing ammonia where it is needed would reduce the additional energy normally used to transport it. Carbon dioxide emissions can be cut even further by using solar-powered lasers, the team adds.
Put this in context
Discover the role of sustainability manager, Mike, who works with businesses and chemists to advise them on being more sustainable.
This article is adapted from Fernando Gomollón-Bel’s in Chemistry World.
Nina Notman
Reference
H Wang et al, Nat. Commun., 2023, 14, 5668 (https://doi.org/10.1038/s41467-023-41441-0)
Download this
Summary slide with questions and the article for context when teaching 14–16 classes on the Haber process: rsc.li/46DjUX7
Downloads
Lasers light the way for greener ammonia production student sheet
PDF, Size 0.16 mbMaking ammonia production greener summary slide
Presentation | PDF, Size 0.19 mbLasers light the way for greener ammonia production student sheet
Word, Size 0.48 mbMaking ammonia production greener summary slide
Presentation | PowerPoint, Size 0.3 mb
References
H Wang et al, Nat. Commun., 2023, 14, 5668 (https://doi.org/10.1038/s41467-023-41441-0)
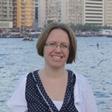
No comments yet