Scientists use semi-permeable polymer membrane and reverse osmosis to separate hydrocarbons and save energy
-
Download this
Use this story and the accompanying summary slide for a real-world context when teaching fractional distillation or reverse osmosis to your 14–16 learners.
Download the story as MS Word or PDF and the summary slide as MS PowerPoint or PDF.
A new polymer membrane that can separate the hydrocarbons in crude oil could potentially save huge amounts of energy by removing the need for fractional distillation. The membrane is similar to the reverse osmosis membranes scientists use to desalinate seawater, meaning its manufacture is potentially scalable to the large volumes that the petrochemical industry would need.
Crude oil is a fossil fuel that contains a mixture of hydrocarbons including diesel and gasoline (petrol). Today, refineries use fractional distillation – a process that consumes nearly 1% of global energy and accounts for 6% of the world’s carbon emissions – to separate these hydrocarbons.
Arid and semi-arid countries, including Saudi Arabia, Kuwait and the US, widely use desalination to produce drinking water. In reverse osmosis plants, seawater passes through semi-permeable membranes that filter out the salt and other impurities.
Efficient separation
The idea of using reverse osmosis to separate hydrocarbons has been around a while, but scientists have found it tricky to identify the right polymer for the job. ‘Some of the materials [we tried] worked, but not really satisfactorily,’ says Tae Hoon Lee, a researcher at Sungkyunkwan University in South Korea, who helped develop the new membrane.
In laboratory testing, Tae Hoon and his colleagues found that their membrane design can separate each component of a mixture of naphtha-, kerosene- and diesel-grade fuel with excellent efficiency throughout a seven-day test period.
Future plans
The team is currently developing the membrane manufacturing processes with the goal of commercialising the product. It is also exploring other potential markets for its membrane including in the pharmaceutical and semiconductor industries. ‘There are many places where solvent–solute separations are needed,’ says Zachary Smith, from the Massachusetts Institute of Technology in the US, who led the project.
‘It is just a matter of time before a demonstration [of membrane crude oil fractionation] outside the university occurs,’ says Ryan Lively, a membrane science expert at Georgia Institute of Technology in Atlanta, US, who was not involved in this work. He adds that this new membrane appears promising, but cautions that the technology development is at an early stage.
This article is adapted from Tim Wogan’s in Chemistry World.
Nina Notman
Reference
T H Lee et al, Science, 2025, doi.org/10.1126/science.adv6886
Download
Summary slide with questions and the article for context when teaching 14–16 lessons on fractional distillation or reverse osmosis: rsc.li/4kijTP1
Downloads
Polymer membrane separates hydrocarbons student sheet
Handout | PDF, Size 0.2 mbPolymer membrane separates hydrocarbons summary slide
Handout | PDF, Size 0.3 mbPolymer membrane separates hydrocarbons student sheet
Editable handout | Word, Size 0.56 mbPolymer membrane separates hydrocarbons summary slide
Editable handout | PowerPoint, Size 1.44 mb
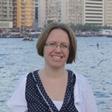
No comments yet