Cutting the huge carbon footprint of fertiliser production
-
Download this
Use this story and the accompanying summary slide for a real-world context when studying the Haber process and fertilisers with your 14–16 learners.
Download the story as MS Word or PDF and the summary slide as MS PowerPoint or PDF.
Researchers in China have developed an efficient way of pulling nitrate from thin air. The electrochemical process could enable a less energy-intense way to produce agricultural fertilisers.
People use nitrate (NO3-) in a variety of products including fertilisers, pharmaceuticals and explosives. Current nitrate production relies on energy-intensive industrial processes, including the Haber and Ostwald processes. The Haber process reacts nitrogen and hydrogen gas at temperatures of around 400°C and pressures of up to 300 atmospheres to form ammonia. The Ostwald process oxidises ammonia to nitric oxide at scorching temperatures of around 800°C. Due to nitrogen’s highly stable triple bond, it has proven difficult to develop sustainable production methods that don’t require such high temperatures or pressures.
Fixing nitrate production
The study’s lead author Kai Dong says his interest in exploring a more sustainable way to oxidise nitrogen was sparked by the hefty environmental drawbacks of traditional methods. ‘That’s where electrochemical nitrogen oxidation comes in,’ Kai says. The reaction occurs at room temperature and pressure and involves applying an electric current or potential difference between electrodes to generate reactive oxygen species from water – these species then oxidise nitrogen in air to nitrate.
Prior attempts to develop electrochemical nitrogen oxidation to fix nitrogen have failed due to competing side reactions that generate oxygen and reduce the efficiency of the reaction, contaminate the nitrate and degrade the electrodes. Kai and his team tweaked the reaction using an electric current to decompose hydrogen peroxide, instead of water, into the necessary reactive oxygen species. The researchers found that this approach was not hindered by the unwanted side reaction issues seen when using water.
To further reduce the environmental impact of its nitrate production process, the team used renewable electricity as its power source. While Kai is optimistic about the future of this process, he says that ‘further research and development efforts are needed to realise its full potential on an industrial scale’.
This article is adapted from Victoria Corless’s in Chemistry World.
Nina Notman
Reference
K Dong et al, Nat. Synth., 2024, 3, 763–773 (doi.org/10.1038/s44160-024-00522-8)
Download
Summary slide with questions and the article for context when teaching 14–16 lessons on the Haber process and fertilisers: rsc.li/3LHcw4C
Downloads
Making nitrates electrochemically summary slide
Presentation | PDF, Size 0.39 mbMaking nitrates electrochemically summary slide
Presentation | PowerPoint, Size 0.79 mbMaking nitrates electrochemically student sheet
Handout | PDF, Size 0.21 mbMaking nitrates electrochemically student sheet
Handout | Word, Size 0.91 mb
Additional information
Saoirse 2013/Shutterstock
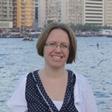
No comments yet