What happens when we need to wind down our wind farms?
-
Download this
Use this story and the accompanying summary slide for a real-world context when studying thermosets and polymers with your 14–16 learners.
Download the story as MS Word or PDF and the summary slide as MS PowerPoint or PDF.
Wind turbines are essential for producing renewable energy but they don’t last forever. In the past, it was not an option to recycle the end-of-life blades, which ended up in landfill sites. The problem is so severe that several European countries have banned dumping the blades in landfill. However, Danish researchers have discovered a new way to recycle wind turbine blades using a specially designed catalyst.
Wind energy contributed to approximately 6% of the global energy supply in 2020, but it is estimated that 43 million tonnes of decommissioned turbine blades will accumulate by 2050. A very small percentage of the old blades is shredded and used as filler in construction materials.
The thermoset plastic blades are made by embedding glass or carbon fibres in a crosslinked epoxy polymer resin. The lightweight, fibre-reinforced materials are also crucial for constructing cars, boats and aircraft. The crosslinking gives the strength needed to withstand large forces but also prevents the materials from being melted down or dissolved.
Freeing fibres
The research team from Aarhus University designed a ruthenium-based catalyst to break carbon–oxygen (C–O) bonds in the epoxy resins. The discovery is perfectly timed. ‘None of the large commercial wind farms have been decommissioned yet, so most deactivated blades aren’t there yet but coming soon,’ says Alexander Ahrens from the university’s Interdisciplinary Nanoscience Center.
The catalyst teases the polymers apart so that high-quality fibres can be reused to make new materials. The method also recovers the petrochemical bisphenol A (BPA), which is harmful to humans and the environment. Retrieving it prevents its potential leakage from landfill sites. Alexander suggests reintroducing the recovered BPA into existing production chains as an alternative to using virgin BPA produced from a petrol-based feedstock.
The catalytic method targets C–O single bonds next to BPA by heating them with the solvents isopropanol and toluene at 160°C. ‘It’s a slow process, so it takes around three days, but in this time the polymer is completely disassembled,’ Alexander says. The team has tested its technique on commercial materials, including a piece of wind turbine blade. After three days it visibly separated into loose fibres, with half safely recovered.
The researchers say that their catalytic process can be considered as a proof-of-concept demonstration of circular economy. ‘The method works on commercial materials being used right now’, says Alexander. However, it requires large amounts of catalyst, which is ‘problematic’ because ruthenium is an expensive and rare transition metal, he adds. The researchers hope it will be possible to redesign the catalyst so that smaller amounts produce the same results. ‘Only if that is possible would upscaling be viable,’ cautions Alexander.
Travis Williams at the University of Southern California, is ‘excited to see that the chemistry community is starting to look more seriously at the problem of thermoset recycling, especially as the retirement of the first generation of carbon fibre epoxy composite aircraft is approaching.’
Put this in context
Discover how sustainability manager, Mike works with businesses and chemists to advise them on being more green through effective recycling and sustainable processes.
This article is adapted from Rebecca Trager’s in Chemistry World.
Emma Davies
Reference
A Ahrens et al, Nature, 2023, 1-8 (DOI: 10.1038/s41586-023-05944-6)
Download this
Summary slide with questions and the article for context when teaching your 14–16 classes on thermosetting polymers:
Downloads
EiC summary slide Recyling wind turbine blades
Presentation | PDF, Size 0.28 mbEiC summary slide Recyling wind turbine blades
Presentation | PowerPoint, Size 1.58 mbEiC science research story Recycling wind turbine blades
Handout | PDF, Size 0.21 mbEiC science research story Recycling wind turbine blades
Handout | Word, Size 0.85 mb
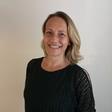
No comments yet