Enhance your teaching of materials and explore how new types of concrete could reduce carbon emissions
Concrete is the most used material on Earth. As materials expert Chris Cheeseman, from Imperial College London, explains: if you could put everything in the world made from concrete in one pile and everything made from other materials in a pile next to it, ‘the concrete pile would dwarf the other pile’.
It’s an unappreciated wonder material. Made from stones, sand and water, its key ingredient, cement, performs some chemical trickery that turns grey, runny slurry into solid rock, in whatever shape we choose. From plant pots to Ancient Rome’s Colosseum, it created the modern world.
In your class
Use this article and the accompanying resources to enhance teaching of the properties and uses of materials. Concrete provides a familiar example of a composite material, but it has a large carbon footprint. This article introduces students to the work scientists around the world are doing to make its production and use more sustainable.
There’s no doubt the building industry would be lost without it. But concrete production is responsible for almost 7% of all carbon emissions. Cement – the paste that binds concrete together and is its key chemical component – is responsible for the majority (80%) of emissions, even though it only makes up around 10% of the mixture. Ordinary Portland cement is made from limestone, clay and other materials that form calcium silicates when heated to high temperatures (around 1500 ºC). This is how concrete ‘sets’. But heating limestone, which is mostly calcium carbonate (CaCO3), also produces a lot of carbon dioxide (CO2).
The other components of concrete – the bigger stones and sand particles (aggregates) – produce much less carbon, so when cement is mixed into concrete, its carbon emissions per kg are actually fairly low at 0.1 kg carbon per kg of cement. ‘That is, in a way, quite sustainable,’ says Veronica Ferrandiz-Mas, who works on innovative construction materials at the University of Bath. ‘But you can improve if it if you improve what you do with the cement.’ And we do need to, simply because we’re making so much of it.
Download this
Worksheets, for age range 14–16
Differentiated worksheets comprising synoptic questions linked to the topic of concrete. Use these worksheets to assess students’ recall of prior learning and identify topics for targeted revision. You can download the high demand version MS Word or pdf and low demand version MS word or pdf.
Differentiated worksheets comprising synoptic questions linked to the topic of concrete. Use these worksheets to assess students’ recall of prior learning and identify topics for targeted revision. Download a high demand and low demand version of the worksheet with answers from the Education in Chemistry website: rsc.li/2NUInB0
So how can we make cement, and therefore concrete, more sustainably? We can add other materials that produce less CO2 to the mix – even if some Portland cement still has to be used to drive the important setting reaction. One example is a steel production by-product called ground granulated blast-furnace slag (GGBS), which can be incorporated in varying quantities up to about 50%. ‘That’s something that cement factories are already using,’ Veronica says, noting that using GGBS not only releases less CO2, but that cements incorporating it are stronger and have a lower risk of cracking because they set at lower temperatures. Using GGBS also gives a useful application to a waste product.
The same can be said for fly ash, a by-product from the coal industry. Although as Chris points out, ‘we’re moving away from coal-fired power stations so the source of fly ash will become difficult.’ There are, however, other materials that could be added. These types of materials, which react with the calcium compounds in cement, are often called pozzolans. They can’t form cement on their own, but they will make cement-like materials if mixed with Portland cement.
Developing countries now need a lot of concrete and they don’t always have the facilities that we do to make it
The leading pozzolan of the future could be calcined clay. Clay is found all over the world and dug up in vast quantities during construction projects like railways. It is ‘calcined’ by heating to a lower temperature (700–850 ºC) than Portland cement, meaning less energy is used. At the Swiss Federal Institute of Technology, calcined clay has become a hot topic for research – researchers there have developed LC3 (limestone calcined clay cements) and trialled production in developing countries including Cuba and India.
‘That is currently a big line of research,’ says Veronica. ‘Because developing countries now need a lot of concrete and they don’t always have the facilities that we do to make it.’ According to Swiss researchers, it is possible to make concrete with calcined clay using the same equipment as in the traditional process. However, unless it’s produced on a large scale, it will be much more expensive.
Chris also has other ideas for improving the sustainability of cement, like incorporating dried, crushed wood – he says this could trap carbon sequestered by trees, effectively rendering concrete carbon-negative. Though he admits it’s not something he’s devoted much except brain power to. ‘I know it’s totally crazy,’ he says. ‘I haven’t done research on it, but it’s certainly something I’m interested in doing.’ He’s also been thinking about how to incorporate shells, like mussel shells or snail shells, into building materials – for their CaCO3 component, toughness and exquisite structure.
In the USA, what might sound like a crazy idea – a concrete replacement you can ‘grow’ on-site – is already a reality. North Carolina-based bioMASON combines waste aggregates or sand with bacteria and water containing calcium ions to make CaCO3-containing stone blocks that set without heating to high temperatures while producing zero CO2 emissions. ‘The final product, post-biological reaction, is most similar to a natural stone,’ says bioMASON director of sales and marketing, Justin Jarman. He says the material is stronger than concrete blocks.
The production of this stone is based on the crystallisation of CaCO3 in corals, suggesting that the natural world could provide a rich source of inspiration for new building materials. However, as Veronica and Chris point out, the most successful materials in the near future are likely to be ones that can be made using existing processes. After all, we’ve been making concrete the same way since the Romans.
This article was updated to include articles on RAAC, 25 March 2024.
Article by Hayley Bennett, a science writer based in Bristol. Resource by Catherine Smith, a teacher at Hinckley Academy and John Cleveland Sixth Form Centre in Leicestershire
More recommended resources
- Provide an opportunity for students to investigate the chemistry of limestone and its relevance in the manufacture of plaster and cement in this practical activity .
- In this practical activity from the Inspirational chemistry series, students investigate how changing the additives in concrete can change its properties. The accompanying written activity provides a comprehensive introduction to composite materials.
- For an interesting anecdote this Soundbite describes the role sugar played in cleaning up a concrete flood in Victoria Station.
- Teachers wishing to further enhance their teaching of the materials topic can try this CPD course.
- Use these articles from Chemistry World to introduce RAAC to this topic: Understanding chemistry in RAAC and Why Roman concrete is still stronger than RAAC
- Add context with our short careers videos showing how chemistry is making a difference.
- Inspire learners and discover more ways chemists are making a difference to our world with our job profiles.
- Provide an opportunity for students to investigate the chemistry of limestone and its relevance in the manufacture of plaster and cement with the thermal decomposition of calcium carboanate: rsc.li/3gkOPxx
- In this practical activity from the Inspirational chemistry series, students investigate how changing the additives in concrete can change its properties. The accompanying written activity provides a comprehensive introduction to composite materials: rsc.li/38r5hJD
- For an interesting anecdote this Soundbite describes the role sugar played in cleaning up a concrete flood in Victoria Station: rsc.li/2VEoDWE
- Teachers wishing to further enhance their teaching of the materials topic can try the Royal Society of Chemistry’s Materials chemistry CPD course: https://rsc.li/2VJrVIf
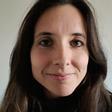
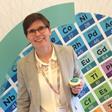
No comments yet